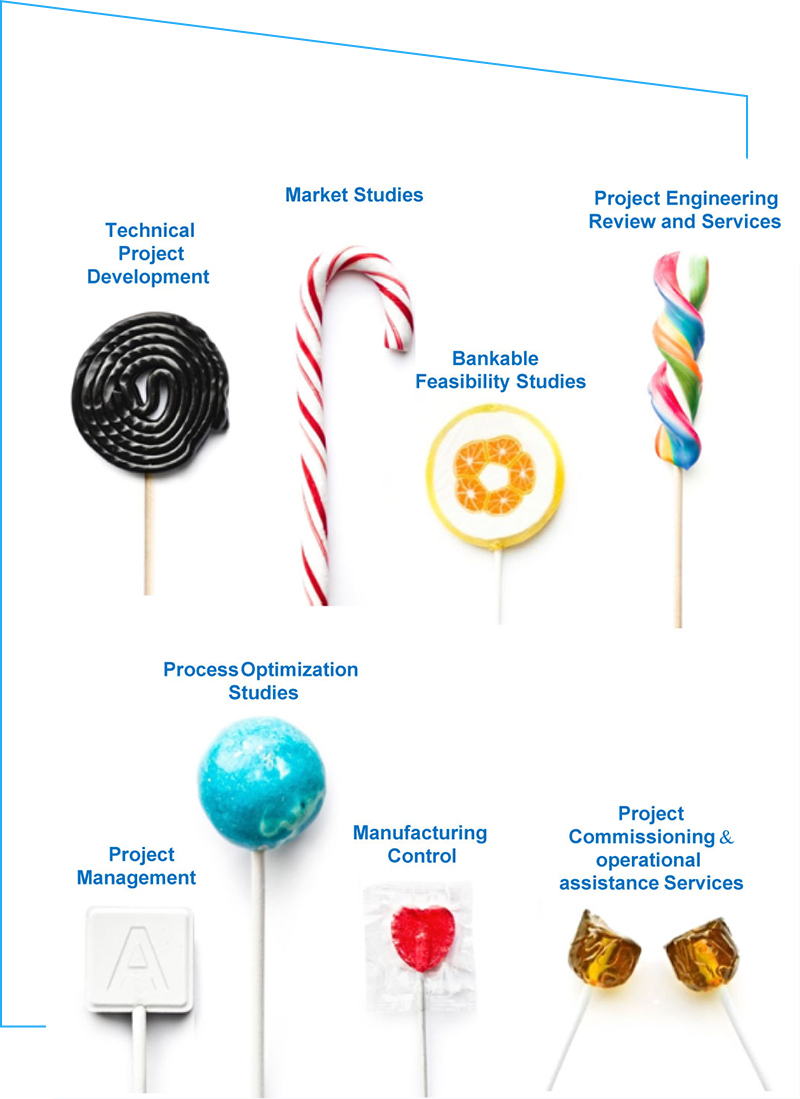
Consulting
NPT - Not just another…
At NPT, we have made a choice. We do not want to be just another consulting company.
We cover specifically those technological areas where we have a deep understanding of the technological processes, markets, products and raw materials, challenges and possibilities and where we can provide full engineering solutions.
You´ll get a fully dedicated know-how partner as your wingmate. We engineer recommendations!
The consultancy and project management portfolio of NPT covers the full baskets of candies needed for a successful project implementation, a sustainable improvement process, a solid engineering development and all kind of technical & commercial project management functions.
Project Definition / Pre-operational Activities
Plant Concept Studies
RFQ preparation
Tender Evaluation and Negotiations
Detailed OPEX definition
Detailed Project CAPEX estimations
Bankable Feasibility Studies
Project Execution
Project Management on behalf on behalf of the project sponsor
Basic Engineering Review
RFQ preparation non-process equipment and EPC portion
Liaison Office
Claim Management
Project Time Schedule Management incl. Critical Path Analysis
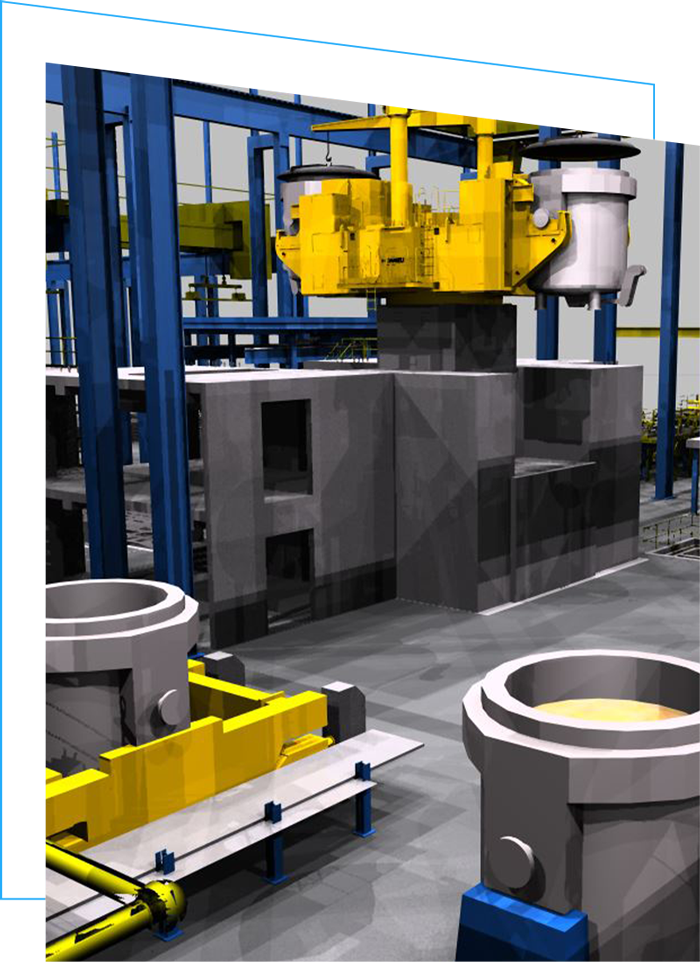
Engineering
We are not clairvoyants.
You can say a lot about our consultants. They are dedicated. Ambitious. Human. And professional people, who have been through demanding engineering processes and projects many times before.But we are not clairvoyants or fortune-tellers. With the right processes, engineering and assessment tools, we can increase the likelihood of finding the most efficient concept and solution for each specific challenge by a in-deep engineering invistigation.That is a responsibility we take seriously and one we are very proud of.
NPT in partnership with its affiliated Engineering Team, is in position to serve the industry with more than 100 highly qualified engineers and draftsmen. Consequently, we can offer a Consulting Set-up which is unique in Europe.Using the most modern software tools the group is capable to execute basic and detail engineering including overall layout engineering of complete plants in 3D and 2D.
Sustainable upfront engineering is crucial and highly feasible for greenfield projects as well as for brownfield / revamping projects. The following picture indicates the risk minimizing impact to project execution when all technical issues are considered and streamlined in the pre-project resp. at the beginning of a major investment project.
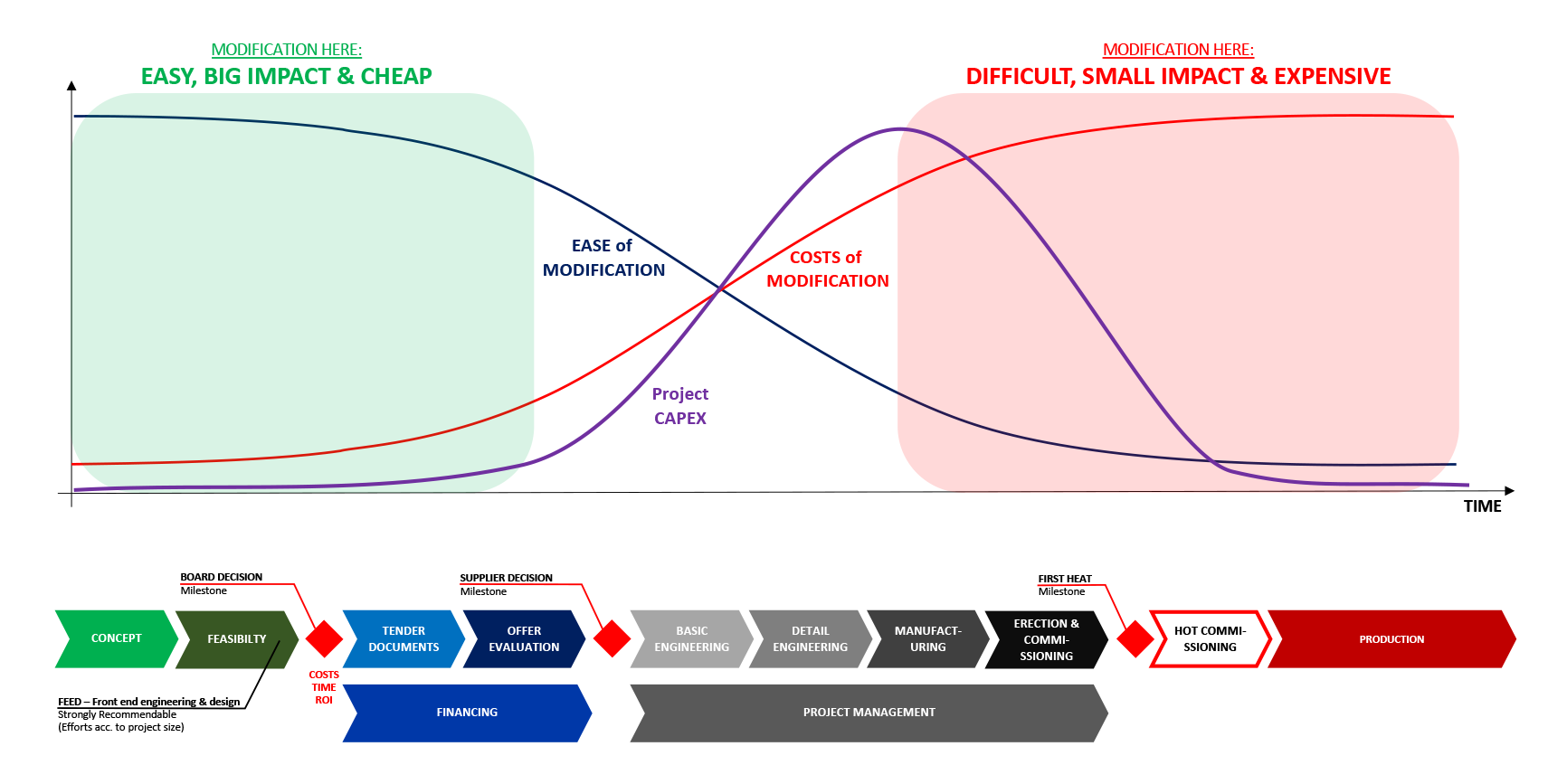
THE CORE PORTFOLIO IS COVERING:
Overall Plant Engineering (BE, DE)
Beneficiation Plants
Pelletizing Plants
DR Plants
Electric Steel Making plants
Complete Mini Mill
Long Product Casting
Long Product Rolling
Integration Facilities (WTP, CAP, Cranes, FTP, etc.)
Equipment Engineering
Electric Arc Furnace (new & revamping)
Secondary Metallurgy (Ladle Furnaces, VD/VOD, RH)
Special Steel Metallurgy
Long Product Casting
Long Product Rolling
Process Engineering
EAF process model
LF process model
VD/VOD/RH process model
SVC & Transformer calculation model
“Utilize the full potential of your investment & assets!”
Steel Plant Logistic Simulation Model
It is of major importance to understand plant logistics at all stages of a project and operation. We can offer to simulate steel plant operation by specific modelling for greenfield, brownfield and operation improvement projects.
GREENFIELD Projects
DESIGN YOUR NEW PLANT'S PERFORMANCE BEFORE YOU INVEST/BUILD IT.
By simulating the complete steel plant logistics with all process interactions and transports/handling activities, we are in position to reliably test if the designed productivity for various production scenarios will be reached. Additionally, we can compare different layout alternatives and machine configuration concepts to further optimize them, so you get the best output from your investment!
BROWNFIELD Projects
TEST THE IMPACT OF NEW EQUIPMENT ON YOUR EXISTING OPERATION.
Brownfield or expansion projects always include a risk that new equipment is not perfectly located or that the existing handling equipment (cranes, transfer cars, etc.) are limiting the performance of the new installation. Unforeseen bottlenecks and limitations in other areas can occur and can negatively influence the envisioned performance. Using upfront simulations can stress test the new configuration and can analyze second or third level consequences.
CONTINUOUS IMPROVEMENT
TEST NEW PRODUCTION PROCEDURES WITH YOUR EXISTING EQUIPMENT.
Production is crucial for every plant. Therefore, it is often difficult to test new process and operational considerations during operation. An upfront simulation can be beneficial and overall, much more feasible to study the affect to a plant or a standard practice without disturbing or interfering production and consequently to have the risk of production losses.
CFD Simulation Model
Using CFD simulation tools, we are able to analyze complex questions and problems involving fluid-fluid, fluid-solid or fluid-gas interaction. This results in a considerable reduction in cost and time for in new designs or proper understanding of process parameter. There is a possibility to analyze different problem whose experiments are very difficult, cost intensive and sometime even dangerous. The CFD modelling offer the capacity of studying system under conditions over its limits.
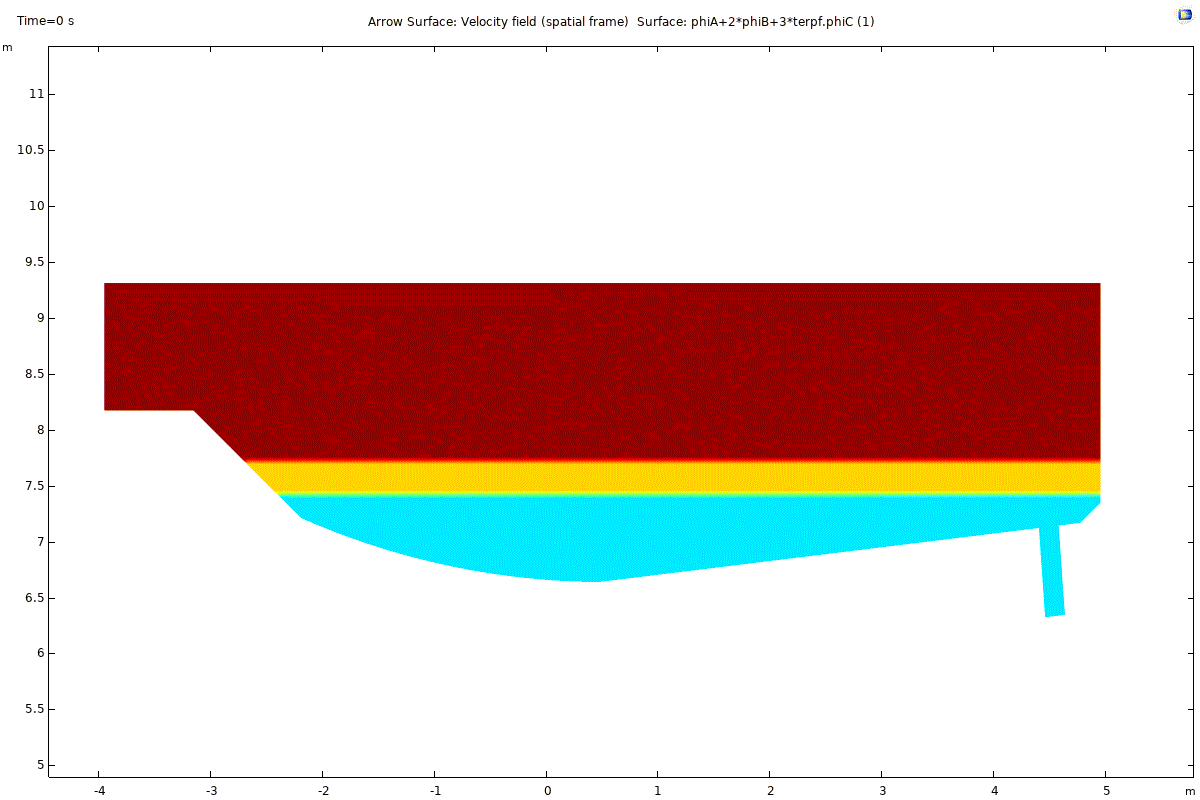